Among various types of steel, medium carbon steel presents unique challenges and opportunities during the welding process. In this article, we aim to provide an accurate, professional, detailed, and authoritative overview of the welding of medium carbon steel.
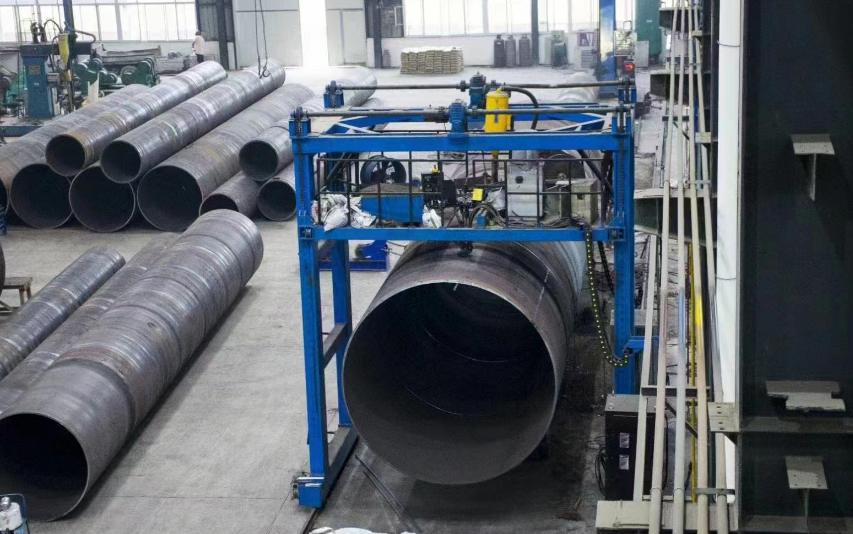
Welding of Medium Carbon Steel – An Overview
1. Properties of Medium Carbon Steel
Medium carbon steel, with a carbon content ranging from 0.30% to 0.60%, offers a balance between strength and ductility. This alloy is widely used in applications that require moderate strength and wear resistance, such as axles, bolts, and shafts. However, the increased carbon content compared to low-carbon steel makes it more susceptible to hardening and brittleness during welding.
2. Welding Methods for the Welding of Medium Carbon Steel
When welding medium carbon steel, it is crucial to choose the right welding method to ensure high-quality welds. Common welding methods include:
2.1 Shielded Metal Arc Welding (SMAW)
SMAW, also known as manual metal arc welding, is suitable for welding medium carbon steel in various positions. It uses a consumable electrode coated with flux to protect the weld pool from atmospheric contamination. This method is versatile and can be used in both indoor and outdoor settings.
2.2 Gas Metal Arc Welding (GMAW)
GMAW, or metal inert gas (MIG) welding, is a semi-automatic or automatic process that uses a continuously fed wire electrode. An inert gas or gas mixture shields the weld pool, preventing contamination. GMAW is suitable for welding medium carbon steel with high production rates.
2.3 Gas Tungsten Arc Welding (GTAW)
GTAW, also known as tungsten inert gas (TIG) welding, is a precise welding method that uses a non-consumable tungsten electrode. An inert gas is used to protect the weld pool, resulting in clean and high-quality welds. GTAW is ideal for welding medium carbon steel in critical applications that require high precision and low distortion.
3. Considerations for the Welding of Medium Carbon Steel
Welding medium carbon steel requires careful consideration of several factors to achieve optimal results.
3.1 Preheat and Postheat Treatment
Preheating the base metal before welding can help prevent cracking by reducing the cooling rate of the weld pool. Postheat treatment, such as stress relief annealing, can further reduce residual stresses and improve the mechanical properties of the weld.
3.2 Welding Materials
Choosing the appropriate welding electrodes, wires, and fluxes is crucial for welding medium carbon steel. The welding materials should match the base metal’s composition and mechanical properties to ensure a strong and ductile weld.
3.3 Welding Parameters
Welding parameters such as current, voltage, and speed significantly affect weld quality. Optimizing these parameters based on the material thickness, welding position, and desired weld properties is essential for achieving high-quality welds.
3.4 Joint Preparation
Proper joint preparation is vital for ensuring good weld penetration and fusion. The joint should be cleaned and prepared according to the specified welding procedure to remove contaminants and impurities that could lead to porosity and weakness in the weld.
Conclusion
Welding medium carbon steel requires a combination of expertise, the right welding method, and attention to detail. Understanding the material’s properties, selecting appropriate welding materials and parameters, and following best practices can lead to high-quality welds that meet the demands of various applications.
Thank you for reading our article and we hope it can help you to have a better understanding of the welding of medium carbon steel. If you are looking for medium carbon steel suppliers online now, please don’t hesitate to contact Huaxia Steel.
As a leading supplier of carbon steel products from Shanghai China, Huaxia Steel provides customers with high-quality carbon steel, tool steel, alloy steel, carbon steel tubes, and carbon steel pipes at a very competitive price.