Tool steel is a crucial component in the manufacturing industry, renowned for its durability, hardness, and wear resistance. Its diverse grades are tailored to meet specific industrial demands, from precision cutting to heavy-duty forming. Here’s a detailed overview of the 6 grades of tool steel.
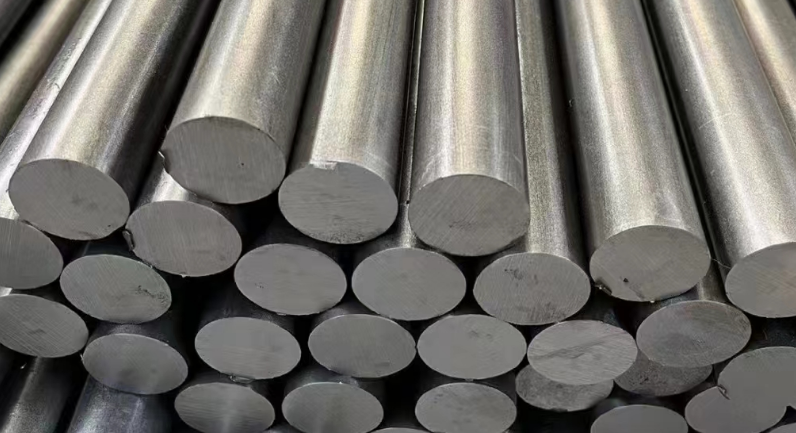
What are the 6 grades of tool steel?
1. Water-Hardening Tool Steel
Water-hardening tool steel, also known as O-series steels, is a low-alloy steel grade. It contains a relatively low carbon content, typically ranging from 0.6% to 1.3%, and small percentages of alloying elements like chromium and manganese. Its primary characteristic is the ability to achieve high hardness when quenched in water, making it suitable for applications that don’t require extreme toughness, such as woodworking tools and cutting tools for soft metals.
2. Oil-Hardening Tool Steel
Oil-hardening tool steel, or W-series steels, offers a balance between hardness, wear resistance, and toughness. It contains higher carbon content, typically ranging from 0.8% to 1.5%, and alloying elements such as chromium, tungsten, and vanadium. These elements enable the steel to achieve excellent hardness when quenched in oil, minimizing distortion during heat treatment. Oil-hardening tool steel is widely used for metal cutting tools, punches, and dies.
3. Air-Hardening Tool Steel
Air-hardening tool steel, represented by the A-series, is a high-alloy steel grade that can achieve high hardness through air cooling after heat treatment. It contains a high carbon content, typically ranging from 0.8% to 1.5%, and alloying elements such as chromium, molybdenum, and vanadium. Air-hardening tool steel exhibits excellent toughness and wear resistance, making it suitable for complex dies, punches, and blanking tools.
4. Hot-Work Tool Steel
Hot-work tool steel, designated as H-series steels, is specifically designed to retain its strength and hardness at elevated temperatures. It contains moderate carbon content and alloying elements like chromium, molybdenum, and vanadium, which improve its resistance to softening and thermal fatigue. Hot-work tool steel is commonly used in die casting, hot forging, and extrusion tools.
5. Cold-Work Tool Steel
Cold-work tool steel, represented by the D-series, is optimized for applications where tools are subjected to high stresses and abrasion at room temperature. It contains a high carbon content, typically ranging from 0.8% to 1.5%, and alloying elements like chromium, tungsten, and vanadium. Cold-work tool steel exhibits excellent hardness, wear resistance, and dimensional stability, making it suitable for cutting tools, dies, punches, and other precision tools.
6. High-Speed Steel (HSS)
High-speed steel (HSS) is a unique grade of tool steel that contains high levels of tungsten, molybdenum, chromium, vanadium, and cobalt. These elements provide exceptional hardness, heat resistance, and wear resistance, enabling HSS to maintain its cutting edge at high temperatures. High-speed steel is widely used in cutting tools, drill bits, taps, and other high-speed machining applications.
Conclusion
In conclusion, the 6 grades of tool steel offer a range of properties tailored to specific industrial demands. From water-hardening steel for basic applications to high-speed steel for high-performance machining, the choice of tool steel grade is crucial for ensuring the performance and durability of tools and dies.
Thank you for reading our article and we hope it can help you to have a better understanding of the 6 grades of tool steel available on the market today. If you are looking for tool steel suppliers and manufacturers online now, we would advise you to visit Huaxia Steel.
As a leading supplier of tool steel products from Shanghai China, Huaxia Steel offers customers high-quality tool steel, carbon steel, and alloy steel at a very competitive price.