Carbon steel, as a ubiquitous metallic material, boasts exceptional mechanical properties, excellent workability, and favorable cost-effectiveness, making it widely used in engineering machinery, automobile manufacturing, petrochemical industries, aerospace, and numerous other sectors. However, its generally poor corrosion resistance limits its application scale significantly due to its vulnerability to factors such as air and water. In this article, let’s take a look at carbon steel’s corrosion resistance and protective measures.
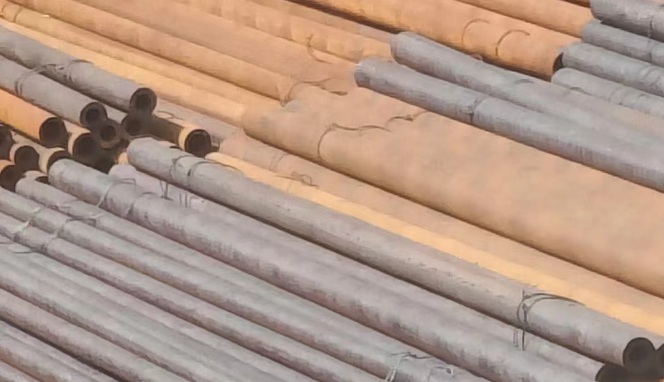
Carbon Steel’s Corrosion Resistance and Protective Measures:
The primary reason for carbon steel’s inferior corrosion resistance lies in its composition, primarily comprising iron and carbon. The iron in carbon steel readily reacts with oxygen and moisture in humid environments, causing the steel surface to lose its shine and texture, eventually leading to rust formation.
To mitigate the impact of corrosion on carbon steel’s service life, effective protective measures must be implemented. Here are some commonly adopted corrosion prevention strategies:
Firstly, coating protection. This is one of the most frequently used methods for carbon steel. Applying protective coatings like paint or resin on the steel surface creates a barrier layer that effectively shields the steel from air and water vapor, thereby preventing rust formation and achieving notable corrosion resistance.
Secondly, electrochemical protection. This technique utilizes electrochemical principles to combat corrosion and safeguard metals. Methods such as anodic protection and cathodic protection can form a protective film on the metal surface, slowing down or preventing corrosion and damage, thus protecting carbon steel equipment, pipelines, and other components.
Thirdly, electroplating. This includes processes like zinc plating, nickel plating, and chrome plating. Zinc plating, for instance, involves depositing a layer of zinc on the carbon steel surface. This zinc layer can form a non-soluble oxide and alkaline salt that effectively isolates the steel from direct contact with the external environment, thereby preventing corrosion. This treatment not only reduces costs but also ensures stable performance over extended periods.
Furthermore, physical protection. This involves utilizing physical means to reduce the impact of corrosive factors or form protective films to prevent corrosion. Techniques like sandblasting, corrosion-resistant linings, and wrapping methods can significantly decrease the environment’s corrosive effects on steel.
Lastly, regular inspection and maintenance. Regularly inspecting and maintaining carbon steel equipment can promptly identify scratches, dirt, and other imperfections on the steel surface. This timely intervention prevents scratches and dirt from reacting with air to cause rust, ensuring a longer service life for carbon steel equipment.
Conclusion
In conclusion, carbon steel, despite its widespread application, often encounters corrosion and rust issues during use. By implementing necessary protective measures, we can not only mitigate these corrosion problems but also reduce maintenance costs and enhance economic efficiency.
Why Choose Huaxia Steel?
Thank you for reading our article and we hope it can help you to have a better understanding of carbon steel’s corrosion resistance and protective measures. If you are looking for suppliers and manufacturers of carbon steel online now, we would advise you to visit Huaxia Steel.
As a leading supplier of carbon steel from Shanghai China, Huaxia Steel offers customers high-quality LOW -CARBON STEEL, MEDIUM CARBON STEEL, and HIGH CARBON STEEL at a very competitive price.