Tool steel, an exceptionally high-performance alloy material, primarily comprises carbon, manganese, phosphorus, sulfur, iron, along with alloying elements such as tungsten, molybdenum, chromium, and vanadium. These elements, particularly tungsten, molybdenum, chromium, and vanadium, play crucial roles in the secondary hardening of tool steels, imparting exceptional physical and chemical properties.
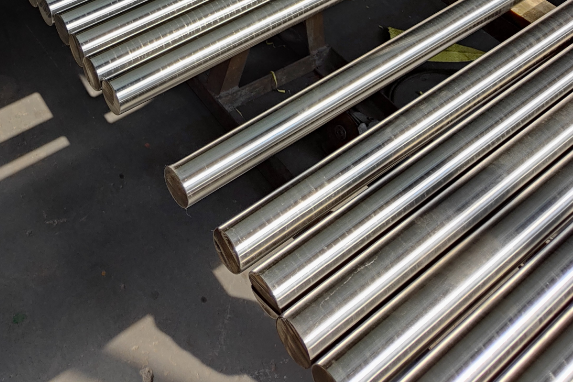
The Role of Tungsten, Molybdenum, Chromium, and Vanadium Alloying Elements in the Secondary Hardening of Tool Steels:
Firstly, tungsten plays an irreplaceable part in the secondary hardening of tool steels. The addition of tungsten facilitates the formation of stable carbides within the steel matrix, primarily in the form of tungsten carbides. These carbides significantly enhance the hot hardness of tool steels during the secondary hardening process. Furthermore, tungsten partially dissolves in the matrix, forming solid solution strengthened alloys that markedly accelerate the secondary hardening process during heat treatment.
Secondly, molybdenum is another vital alloying element that contributes to the secondary hardening of tool steels. Molybdenum forms high-melting-point molybdenum carbides with carbon, which promotes secondary hardening. This enables better formation of martensite during quenching, thereby improving the hardness, creep resistance, and thermal stability of tool steels. Additionally, molybdenum enhances the corrosion resistance of tool steels in specific media, enabling them to maintain excellent corrosion resistance during the secondary hardening process, broadening their applicability in corrosive environments.
Furthermore, vanadium exhibits a strong affinity with carbon. The addition of 0.15% to 1% vanadium to tool steels forms stable vanadium carbides, enhancing the hardness and density of the steel. Vanadium also improves the tempering stability of tool steels by partially dissolving the formed carbides into austenite during heating. Upon tempering, these carbides precipitate as fine particles, causing secondary hardening, thereby increasing the red hardness of tool steels.
Lastly, chromium serves as a crucial alloying element in tool steels. It refines the steel structure, ensuring a uniform distribution throughout the steel volume. Chromium forms high-melting-point chromium carbides with carbon, which not only increase the hardness and wear resistance of tool steels during secondary hardening but also enhance their hardenability, reducing distortion during quenching. Additionally, chromium forms an oxide film on the steel surface, improving its corrosion resistance.
Conclusion
In conclusion, the secondary hardening process of tool steels is a pivotal stage, and different alloying elements play distinct roles in this process. Therefore, selecting appropriate alloying elements and controlling their content judiciously is essential to ensure optimal performance of tool steels based on specific tool and die requirements.
Why Choose Huaxia Steel?
Thank you for reading our article and we hope it can help you to have a better understanding of the role of tungsten, molybdenum, chromium, and vanadium alloying elements in the secondary hardening of tool steels. If you are looking for suppliers and manufacturers of tool steel, we would advise you to visit Huaxia Steel.
As a leading supplier of tool steel from Shanghai, Huaxia Steel offers customers high-quality tool steel at a very competitive price.