The Relationship Between Carbon Steel and Tool Steel
Carbon steel and tool steel are two fundamental types of steel, each with its own specific properties and applications. While they share some similarities—both being forms of steel with varying carbon content—they serve very different purposes in industrial and manufacturing contexts. Understanding the relationship between carbon steel and tool steel can help clarify their unique roles and why each is chosen for specific applications.
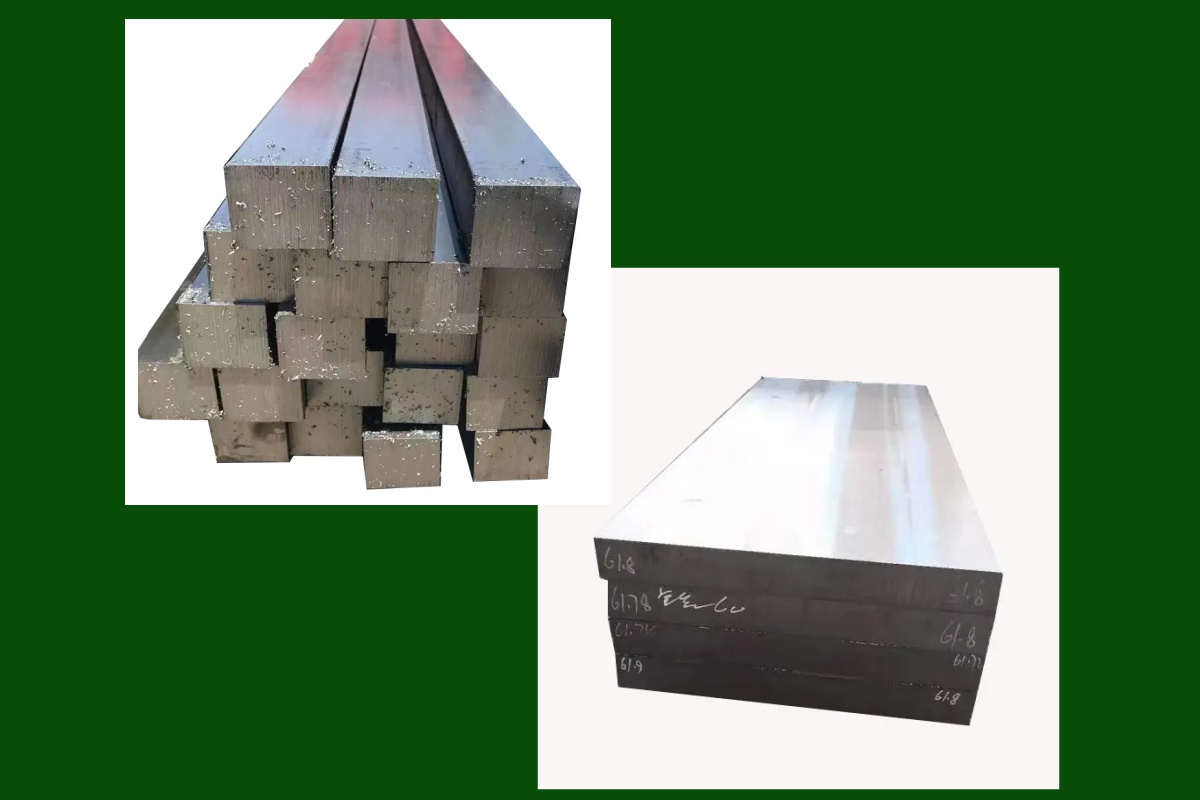
What Is Carbon Steel?
Carbon steel is a broad category of steel where carbon is the primary alloying element. The carbon content in carbon steel typically ranges from 0.05% to 2.1%, which affects its hardness, strength, and ductility. Carbon steels are classified into different categories based on their carbon content:
- Low Carbon Steel (Mild Steel): Contains less than 0.3% carbon. It’s soft, ductile, and easy to shape, making it ideal for structural applications such as beams, plates, and machinery parts.
- Medium Carbon Steel: Contains between 0.3% and 0.6% carbon, providing a good balance of strength and ductility. It’s used in automotive parts, axles, and gears.
- High Carbon Steel: Contains between 0.6% and 1.5% carbon, making it hard and strong but less ductile. This steel is often used for springs, knives, and high-strength wires.
The primary characteristics of carbon steel are its affordability, strength, and ease of processing, making it a versatile choice for many industries, particularly construction and manufacturing.
What Is Tool Steel?
Tool steel is a specialized type of steel designed specifically for manufacturing tools, cutting equipment, and dies. Tool steels are typically alloyed with additional elements like tungsten, chromium, molybdenum, and vanadium. These elements give tool steel its hardness, resistance to wear, and ability to retain sharpness at high temperatures. Tool steels are categorized based on their working environment:
- Cold-work Tool Steel: Used for tools that operate at low temperatures (e.g., punches, dies, and blades).
- Hot-work Tool Steel: Designed for tools that endure high temperatures, like die-casting molds and forging dies.
- High-speed Steel (HSS): Capable of cutting materials at high speeds without losing its hardness, often used in drills, cutting tools, and saw blades.
Tool steel is engineered to maintain its strength and hardness under heavy use and in extreme conditions, which makes it ideal for tasks that involve cutting, shaping, and forming other materials.
How Carbon Steel and Tool Steel Are Related?
While tool steel and carbon steel share a common base—both are forms of steel—the key difference lies in the specific alloying elements and processing methods used to create each. Here’s how they are related and differ:
Carbon Content:
- Tool steel can be considered a subset of high-carbon steel because it contains a significant amount of carbon, often above 0.6%, which contributes to its hardness and strength.
- Carbon steel, on the other hand, is a broader category that includes low, medium, and high carbon steels. High carbon steel overlaps with tool steel in terms of carbon content, but without the additional alloying elements that tool steel has.
Alloying Elements:
- While carbon steel mainly relies on carbon to achieve strength, tool steel is alloyed with additional elements like chromium, vanadium, and tungsten to enhance its wear resistance, toughness, and heat resistance. These alloying elements are what allow tool steel to retain its cutting edge and shape in extreme conditions.
- Carbon steel, especially in its lower grades, does not have these alloying elements, making it less suitable for high-performance applications like cutting or drilling.
Hardness and Durability:
- Tool steel is specifically designed to be much harder and more durable than carbon steel. Through heat treatment processes like quenching and tempering, tool steel achieves a superior hardness that allows it to withstand constant friction and impact without deforming.
- Carbon steel can be hardened, especially in higher-carbon forms, but it generally lacks the same wear resistance and toughness under extreme conditions.
Applications:
- Carbon steel is widely used in structural applications like buildings, bridges, and automotive parts. Its affordability and ease of fabrication make it ideal for use in construction and manufacturing.
- Tool steel is essential in manufacturing tools, dies, cutting equipment, and molds. It is found in high-performance applications where precision, toughness, and heat resistance are required, such as machining, metalworking, and die-casting.
Conclusion
While carbon steel and tool steel are related, they serve very different purposes due to their distinct alloy compositions and properties. Carbon steel is a versatile and cost-effective material used in structural and general manufacturing applications, whereas tool steel is a highly specialized material designed for demanding tasks like cutting, shaping, and forming other materials. The added alloying elements and heat treatments used in tool steel make it far more durable and heat-resistant than standard carbon steel, making it indispensable in industries requiring high precision and toughness.
Understanding the relationship between these two types of steel is key to selecting the right material for your project, whether it’s constructing a building or manufacturing precision tools.
FAQs about the relationship between carbon steel and tool steel
No, tool steel is not the same as carbon steel, although both are types of steel. The main difference lies in their composition and intended use:
Carbon steel is primarily composed of iron and carbon, with carbon content typically ranging from 0.05% to 2.1%. It is commonly used in structural applications, such as building construction, automotive parts, and manufacturing.
Tool steel is a specialized type of high-carbon steel with added alloying elements like tungsten, chromium, vanadium, and molybdenum, which improve its hardness, toughness, and heat resistance. Tool steel is specifically designed for cutting tools, dies, and molds where resistance to wear and deformation is critical.
While tool steel contains carbon and shares some similarities with high-carbon steel, its enhanced properties make it suitable for demanding applications that carbon steel alone cannot handle.
The relationship between carbon and steel is fundamental. Carbon is the key element that determines the hardness, strength, and flexibility of steel:
Low carbon content (less than 0.3%) results in softer, more ductile steel, which is easy to shape and weld. This type is called mild steel.
Medium carbon content (0.3% to 0.6%) increases the strength and hardness of the steel, making it useful for structural components like gears and axles.
High carbon content (above 0.6%) results in hard, brittle steel that can be heat-treated for high strength and wear resistance. This type of steel is often used for tools and cutting instruments.
As carbon content increases, steel becomes harder and stronger but also more brittle. The balance between hardness and toughness is key to the performance of various types of steel.
Tool steel typically contains 0.5% to 1.5% carbon, depending on the specific type and its intended application. This high carbon content gives tool steel its hardness and strength, which are essential for cutting, shaping, and forming tools.
In addition to carbon, tool steel also includes other alloying elements like chromium, tungsten, vanadium, and molybdenum, which improve its performance in high-wear and high-temperature environments. The carbon and alloy content allows tool steel to retain sharpness and resist wear over time.
The main difference between carbon steel and stainless steel is the amount of chromium:
Carbon steel primarily contains iron and carbon, with little to no chromium. It is strong and durable but prone to rust when exposed to moisture because it lacks the protective layer that chromium provides.
Stainless steel contains at least 10.5% chromium, which forms a protective oxide layer on the surface, making it highly resistant to corrosion and rust. Stainless steel may also contain other alloying elements like nickel and molybdenum to enhance its properties.
While carbon steel is used for its strength and affordability, stainless steel is valued for its corrosion resistance and ability to maintain its appearance and structural integrity in harsh environments. Both are widely used in different industries based on their specific characteristics.
Carbon steel and stainless steel can be used together in certain applications, but they are not inherently compatible without special consideration. The two types of steel have different properties due to their compositions, which can lead to issues like galvanic corrosion when they are in direct contact with each other, especially in the presence of an electrolyte like water.
Galvanic corrosion occurs because carbon steel is more likely to corrode when it is electrically connected to stainless steel in a moist environment. To ensure compatibility, protective measures such as coatings, insulators, or proper separation should be used to prevent direct metal-to-metal contact.
Yes, stainless steel can be connected to carbon steel, but there are a few challenges that need to be addressed:
Welding: When welding stainless steel to carbon steel, the differences in the alloying elements (mainly chromium in stainless steel and carbon in carbon steel) require specific welding techniques. Dissimilar metal welding typically requires a filler material that is compatible with both metals to prevent cracking or corrosion at the joint. Common filler materials for this process include 309L or 309LSi welding wire.
Galvanic Corrosion: As mentioned earlier, galvanic corrosion can occur if stainless steel and carbon steel are connected in a moist or corrosive environment. To mitigate this, the metals should be coated or separated with insulating materials to prevent direct contact.
Thermal Expansion: Stainless steel and carbon steel expand and contract at different rates when exposed to heat, which can cause stress at the joint. This needs to be considered during the design process to ensure a durable connection.
If you found this article good, feel free to share it on your other social media platforms.