9310 steel vs 300M are often considered for similar applications due to their exceptional strength and toughness, but they have distinct properties that make them suitable for different scenarios. In this article, we’ll delve into the key differences between 9310 steel and 300M, examining their composition, mechanical properties, applications, and more.
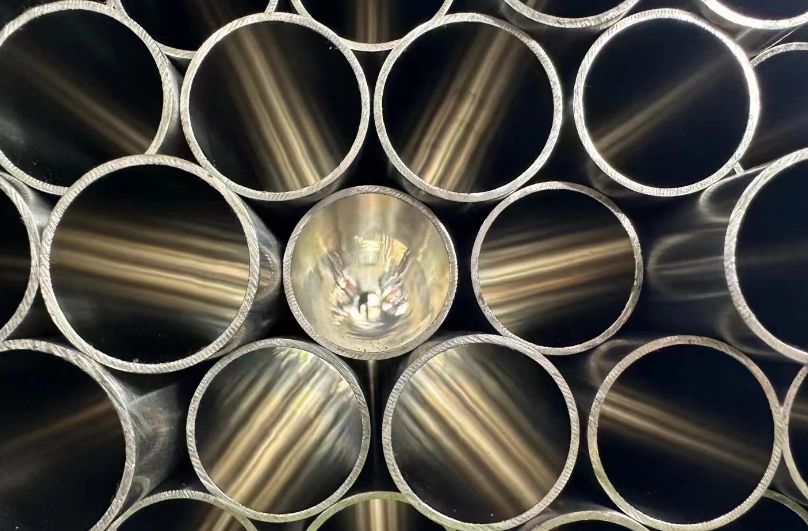
9310 Steel vs 300M – What’s the Difference?
9310 Steel vs 300M – 1. Definition
9310 steel is an air-hardening, low-alloy steel that belongs to the AISI 52100 family. It’s characterized by its high carbon content (approximately 1%) and the addition of chromium, molybdenum, and silicon. This combination of elements gives 9310 steel its unique properties.
300M steel, also known as AISI 4340M, is a low-alloy, vacuum-melted steel that’s been widely used in the aerospace industry for its exceptional strength and toughness.
9310 Steel vs 300M – 2. Composition
Composition of 9310 Steel:
- Carbon: 0.95-1.05%
- Chromium: 1.40-1.60%
- Molybdenum: 0.15-0.30%
- Silicon: 0.20-0.40%
- Manganese: 0.20-0.40%
Composition of 300M Steel:
- Carbon: 0.38-0.43%
- Nickel: 1.65-1.95%
- Chromium: 0.80-1.10%
- Molybdenum: 0.15-0.25%
9310 Steel vs 300M – 3. Mechanical Properties
Mechanical Properties of 9310 Steel:
- High hardness after heat treatment
- Good wear resistance
- Good fatigue strength
- Good impact resistance
Mechanical Properties of 300M:
- High yield strength
- Exceptional fatigue resistance
- Good toughness
- Good weldability
9310 Steel vs 300M – 4. Applications
Applications of 9310 Steel:
9310 steel is commonly used in applications that require high wear resistance and toughness, such as:
- Bearings
- Gears
- Rolling contact fatigue-resistant components
- Race car components (such as axles and shafts)
Applications of 300M:
300M steel is primarily used in high-strength, load-bearing applications where fatigue resistance and toughness are paramount, such as:
- Aircraft landing gear components
- Helicopter rotor blades
- Gun barrels and other weaponry components
- High-performance automotive components
9310 Steel vs 300M – 5. Comparison
Both 9310 steel and 300M steel are high-performance materials with excellent mechanical properties. However, there are some key differences between them:
- Carbon Content: 9310 steel has a higher carbon content, which contributes to its hardness and wear resistance. By contrast, 300M steel has a lower carbon content, allowing for better weldability and toughness.
- Alloying Elements: The addition of nickel in 300M steel enhances its strength and fatigue resistance, making it ideal for high-cycle fatigue applications. 9310 steel, on the other hand, relies on chromium and molybdenum for its wear resistance and hardness.
- Applications: While both materials are used in high-strength applications, 9310 steel is more common in wear-resistant components like bearings and gears, while 300M steel shines in fatigue-critical applications like aircraft components.
Conclusion
In conclusion, 9310 steel and 300M steel are both excellent choices for high-performance applications, but they have distinct properties that make them more suitable for different scenarios.
Thank you for reading our article and we hope it can help you to have a better understanding of the differences between 9310 Steel vs 300M. If you are looking for alloy steel suppliers online now, please don’t hesitate to contact Huaxia Steel.
As a leading supplier of alloy steel from Shanghai China, Huaxia Steel provides our customers with high-quality alloy steel, carbon steel, tool steel, carbon steel tubes, and carbon steel pipes at a very competitive price.