Alloy steel, a steel material cleverly combined by multiple elements, has occupied a pivotal position in the modern industrial field with its unique properties and wide applications. From the engine of a car to the hull of a spacecraft, and to the precision medical equipment, alloy steel is everywhere. So, what are the types, applications, and grades of alloy steel? In this article, we’ll take a close look at alloy steel grades, types & applications.
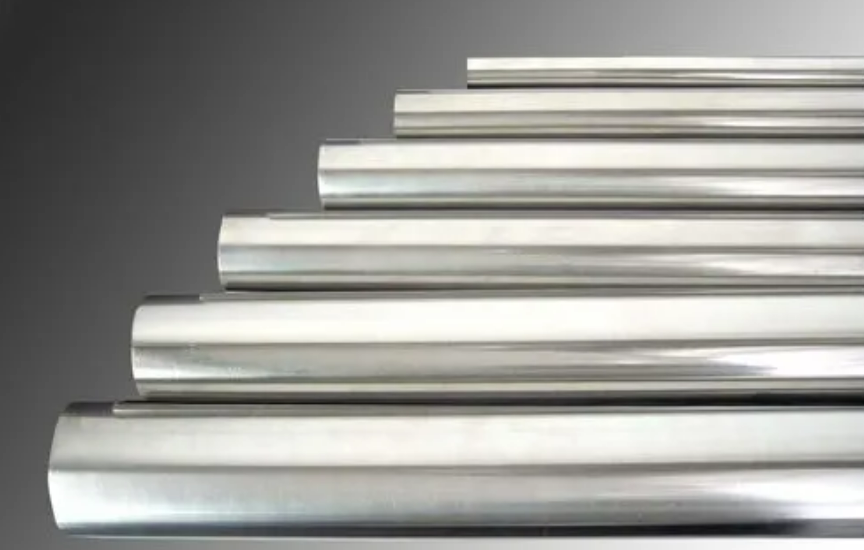
What is alloy steel?
In addition to iron and carbon, if other alloy elements are added to steel, it is called alloy steel. It is an iron-carbon alloy formed by adding a proper amount of one or more alloying elements to the basis of ordinary carbon steel. According to the different added elements and appropriate processing technology, special properties such as high strength, high toughness, wear resistance, corrosion resistance, low-temperature resistance, high-temperature resistance, and non-magnetism can be obtained.
Alloy Steel Grades, Types and Applications:
According to their uses, alloy structural steels are divided into low-alloy high-strength structural steel, carburizing steel, easy-cutting steel, quenching steel, spring steel, and rolling bearing steel.
1.1 Low-alloy High-strength Structural Steel
1.1.1 Compositional Features, Low Carbon, Content Less than 0.2%;
The main alloying element is Mn, less than 3%;
Adding Nb, Ti, V to improve stiffness and toughness, adding Cu, P to improve corrosion resistance;
1.1.2 Typical Grades and Uses
1.1.2.1 Q345 (16Mn), with good comprehensive performance, is the most widely used low-alloy high-strength structural steel. It is used in large steel structures such as vehicles, ships, and bridges;
1.1.2.2 Q390 (15MnV), with high strength, is used for medium-pressure vessels;
1.1.2.3 Q460 (18MnMoNb), with high strength, is used for high-pressure boilers and high-pressure vessels.
1.2 Carburizing Steel
1.2.1 Compositional Features, Low Carbon, Content 0.1%~0.25%;
Adding alloying elements to improve quenching hardenability, Cr, Ni, Mn;
Adding elements that hinder grain growth, Ti, V, W;
1.2.2 Typical Grades and Uses
1.2.2.1 Low quenching hardenability: 20Cr, 15Cr, used for wear-resistant parts with low stress, such as diesel engine piston sheaths and camshafts;
1.2.2.2 Medium quenching hardenability: 20CrMnTi, 20Mn2TiB, used for wear-resistant parts with medium load, such as transmission gears for automobiles/tractors;
1.2.2.3 High quenching hardenability: 18Cr2Ni4WA, 20Cr2Ni4A, used for wear-resistant parts with high load, such as diesel engine crankshafts.
1.3 Easy-cutting Steel
1.3.1 Description
Easy-cutting steel, also known as automatic steel, is used for automatic machine tool processing due to its fast speed and large cutting depth. The dimensions for evaluating easy-cutting steel include service life, cutting force size, roughness of the processed surface, cutting heat, and ease of cutting residue removal.
1.3.2 Compositional Features
To improve cutting performance, S, Pb, Ca, and P are often added.
1.3.2.1 S can make the steel brittle and not adhere to the knife, but it can also cause thermal brittleness in the steel. Therefore, the content should be controlled between 0.08-0.3%, and used in combination with Mn;
1.3.2.2 Pb can reduce the temperature of the knife and wear, and the content should be controlled between 0.1-0.35%;
1.3.2.3 Ca can form high-melting-point complex oxides that attach to the knife edge to prevent wear. The content should be controlled between 0.001-0.005%;
1.3.2.4 P can form Fe-P compounds that facilitate the breakage of cutting residue, but P also has cold brittleness. The content should be controlled between 0.05-0.1%.
1.3.3 Typical Grades and Uses
1.3.3.1 Low-carbon easy-cutting steel: Y12, Y15, Y20 are commonly used to manufacture various machine and instrument parts that require low mechanical properties, such as bolts, nuts, pins, shafts, and pipe fittings;
1.3.3.2 Medium-carbon easy-cutting steel: Y40Mn has high strength and hardness, suitable for processing parts that require high stiffness, such as screw rods, rods, gears, and splines.
1.4 Quenching and Tempering Steel
1.4.1 Description
Quenching and tempering steel is used as important parts of machines and equipment, such as machine tool spindles, engine crankshafts, connecting rods, etc. It requires both high strength and toughness and ductility.
1.4.2 Compositional Features
Medium carbon, 0.25-0.5%;
Add alloying elements to improve quenching hardenability, Cr, Mn, Ni, Si;
Add alloying elements to prevent second-type temper embrittlement, Mo, W;
1.4.3 Typical Grades and Uses
1.4.3.1 Low quenching hardenability: 40Cr, 40MnB, used for important parts of general size, such as gears and spindles;
1.4.3.2 Medium quenching hardenability: 35CrMo, 38CrSi, used for parts with larger cross-sections, such as crankshafts and connecting rods;
1.4.3.3 High quenching hardenability: 37CrNi3, 40CrMnMo, used for parts with larger cross-sections and heavy loads, such as the main shaft and impellers of steam turbines.
1.5 Spring Steel
1.5.1 Description
Spring steel is used for manufacturing springs. It requires good elasticity, fatigue resistance, and corrosion resistance.
1.5.2 Compositional Features
Medium to high carbon, 0.5-0.7%;
Main alloying elements include Mn and Si to improve quenching hardenability;
Spring steel for important applications also requires the addition of Cr, W, and V;
Must be made from high-quality or extra-high-quality steel;
1.5.3 Typical Grades and Uses
1.5.3.1 Silicon/Manganese alloyed: 65Mn, 60Si2Mn, etc., used for buffer coils in freight carriages;
1.5.3.2 Chromium/Tungsten/Vanadium alloyed: 50CrVA, 55CrMnA, etc., used for heavy-duty vehicle plate springs, torsion bars, and springs that can withstand temperatures below 350℃.
1.6 Rolling Bearing Steel
1.6.1 Description
Rolling bearing steel is used for manufacturing rolling bearings. It requires good wear resistance, fatigue resistance, and corrosion resistance.
1.6.2 Compositional Features
High carbon, 0.95-1.15%;
Cr is the basic alloying element, with a content of 0.4-0.65%, which improves quenching hardenability, wear resistance, and fatigue strength;
Addition of Si/Mn to improve quenching hardenability;
Addition of V to improve wear resistance and prevent overheating;
High metallurgical quality; statistics show that 65% of bearing failures are due to inadequate metallurgical quality.
1.6.3 Typical Grades and Uses
1.6.3.1 Cr bearing steel: GCr15. Used for small and medium-sized bearings, cold stamping dies, measuring tools, and threading taps;
1.6.3.2 Bearing steel with added Mn/Si/Mo/V: GCr15SiMn, GCr15SiMnMoV, used for large bearings.
2. Alloy tool steels are classified according to their uses into low-alloy cutting tool steel, high-speed steel, alloy die steel, and alloy gauge steel.
2.1 Low-alloy cutting tool steel
2.1.1 Compositional Features, High carbon, content 0.9-1.1%; addition of Si, Mn, Cr, W, V, etc.;
2.1.2 Typical Grades and Uses. 9Mn2V, 9SiCr, CrWMn, mainly used for threading dies, taps, drills, punching dies, drawknives, and low-speed cutting tools.
2.2 High-speed steel
2.2.1 Compositional Features, High carbon, content 0.7-1.5%; addition of Mo, Cr, W, V, etc.;
2.2.2 Typical Grades and Uses. W18Cr4V, 9W18Cr4V, W6Mo5Cr4V2, mainly used for high-speed cutting tools such as lathe tools, milling cutters, drills, etc.
2.3 Alloy die steel
2.3.1 Compositional Features,
Cold working die steel: High carbon, 1-2%; addition of Cr, Mo, W, V, etc.;
Hot working die steel: Medium carbon, 0.3-0.6%; addition of more alloying elements to improve quenching hardenability such as Cr, Ni, Mn, Si; addition of Mo, W, V to produce secondary hardening.
2.3.2 Typical Grades and Uses.
2.3.2.1 Cold working die steel: 9Mn2V, Cr12, Cr4W2MoV, used for cold compression molds, punching dies, plastic films, cold extrusion dies, etc.;
2.3.2.2 Hot working die steel: 5CrMnMo, 4Cr5MoSiV, 5Cr4W5Mo2V, used for forging dies, hot heading dies, die-casting molds, hot extrusion dies, etc.;
2.4 Alloy gauge steel
There is no dedicated steel grade, and rolling bearing steel, low-alloy cutting tool steel, and stainless steel materials are often used.
2.4.1 Compositional Features, High carbon, 0.9-1.5%; addition of more alloying elements to improve quenching hardenability such as Cr, Mn, W;
2.4.2 Typical Grades and Uses. CrMn, GCr15, CrWMn, used for manufacturing calipers, screw gauges, block gauges, plug gauges, etc.;
Conclusion
Thank you for reading our article and we hope it can help you know alloy steel grades, types, and applications better. If you want to learn more about alloy steels, we would advise you to visit Huaxia Steel.
As a leading supplier of carbon steel across the world, Huaxia Steel provides customers with a wide range of high-quality products such as alloy steel, tool steel, carbon steel, carbon steel tubes, and carbon steel pipes for global markets at a very competitive price.