Alloy steel, as a crucial metallurgical material, primarily comprises alloying elements such as nickel, molybdenum, cobalt, titanium, and others. Compared to ordinary steel, alloy steel undergoes specific smelting methods to significantly enhance its hardness, strength, wear resistance, corrosion resistance, and high-temperature endurance, thereby playing a pivotal role in modern industrial production. In this article, let’s take a closer look at alloy steel smelting processes.
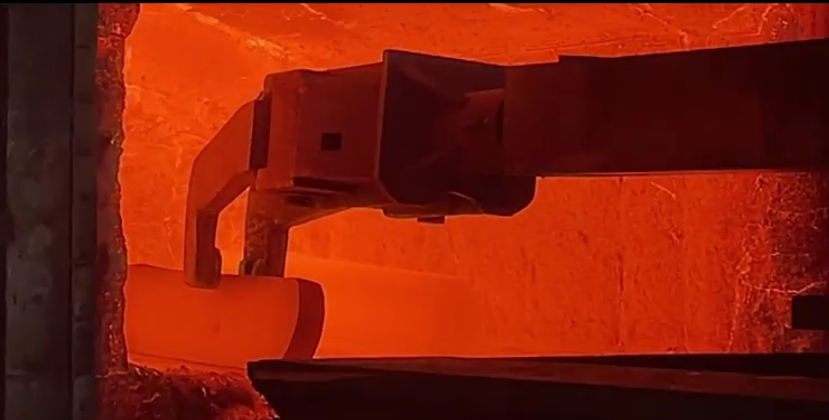
Detailed Explanation of Alloy Steel Smelting Processes:
Firstly, the Electric Arc Furnace (EAF) method is one of the most commonly used smelting techniques for alloy steel. It leverages the heat generated by electric arcs to melt metals and refine them. In this process, scrap steel serves as the primary raw material, while alloys, lime, and carburizers are utilized as auxiliary materials. Apart from its high production efficiency and low smelting cost, the EAF method also allows for precise control and automation.
Secondly, the Electric Furnace Reduction (EFR) method employs electricity as an energy source to reduce metal oxides into metals through high-temperature reactions. Raw materials such as magnesite, dolomite, and rhodonite are predominantly used. This method demands rigorous temperature control since excessively high temperatures can lead to coarse grain structures, affecting alloy steel’s strength and toughness, while excessively low temperatures can drastically decrease its impact toughness, causing low-temperature embrittlement. The EFR method is characterized by simplicity, flexibility, and high utilization rates, effectively reducing energy consumption.
Thirdly, the Basic Oxygen Steelmaking (BOS) process utilizes industrial-grade oxygen blown into the molten bath to chemically react with carbon, silicon, manganese, phosphorus, and other elements, raising the bath temperature and enhancing steel’s conversion rate and quality. The BOS process can be further divided into top-blown, bottom-blown, and side-blown variants, all requiring oxygen purity exceeding 99%.
Furthermore, the Vacuum Smelting method conducts smelting in a vacuum environment. By lowering the ambient pressure and reducing the number of gas molecules, it minimizes the likelihood of metal-gas reactions, preserving the metal’s purity and physical properties. In alloy steel smelting, the Vacuum Smelting method enables precise control over the content of easily oxidized elements, ensuring that alloy steel meets desired performance and quality standards.
Conclusion
In conclusion, alloy steel smelting is a complex process involving multiple methods, including EAF, EFR, BOS, and Vacuum Smelting, along with hybrid steelmaking and combined blowing converter steelmaking. Each method yields alloy steel with distinct properties and qualities. In practical production, selecting the appropriate smelting method based on alloy steel’s specific requirements and application scenarios is crucial to achieve the desired smelting outcomes.
Why Choose Huaxia Steel?
Thank you for reading our article and we hope it can help you to have a better understanding of the alloy steel smelting processes. If you are looking for alloy steel suppliers and manufacturers online now, we would advise you to visit Huaxia Steel.
As a leading supplier of alloy steel from Shanghai China, Huaxia Steel offers customers high-quality alloy steel, carbon steel and tool steel products at a very competitive price.