When it comes to tool steel, the choices can be overwhelming. Two popular options that often find their way into industrial applications are O1 and D2 tool steel. While both are highly regarded for their hardness, durability, and wear resistance, there are distinct differences between them. So, O1 vs D2 tool steel – what’s the difference? In this article, we’ll explore the fundamental differences between O1 and D2 tool steel.
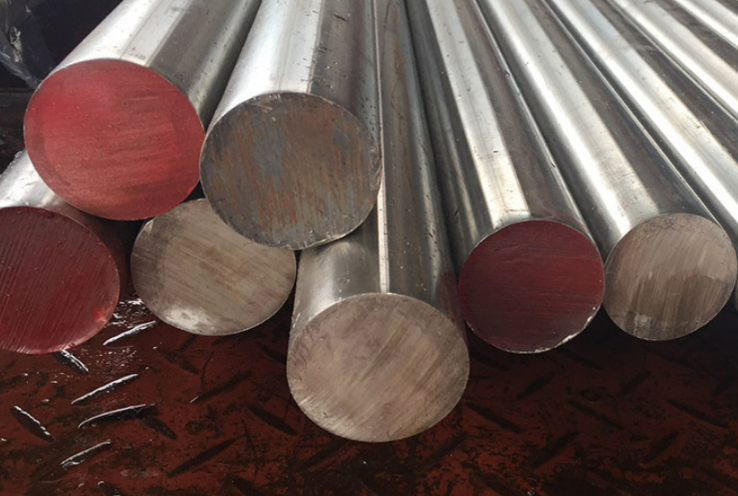
O1 vs D2 Tool Steel – What’s the Difference?
O1 vs D2 Tool Steel – 1. Composition
The fundamental difference between O1 and D2 tool steel lies in their composition. O1, also known as oil-hardening tool steel, is a low-alloy high-carbon steel. It typically contains a carbon range of 0.75% to 0.95%, along with small amounts of manganese, silicon, and chromium. The high carbon content gives O1 its hardness and wear resistance, while the chromium adds some corrosion resistance.
On the other hand, D2 tool steel is a high-carbon, high-chromium steel. It contains a carbon range of 1.40% to 1.60% and a chromium content of approximately 11.5%. The high carbon and chromium content give D2 its exceptional hardness, wear resistance, and resistance to heat and corrosion. D2 also contains small amounts of molybdenum and vanadium, which further enhance its toughness and wear properties.
O1 vs D2 Tool Steel – 2. Heat Treatment
The heat treatment process for O1 and D2 tool steel also differs. O1 steel is typically oil-quenched, which means it is heated to a high temperature and then cooled in oil. This process results in a harder and more wear-resistant steel but with less toughness than air-quenched steels. O1 can also be air-quenched for improved toughness but at a slightly lower hardness.
D2 steel, on the other hand, is usually air-quenched or vacuum-quenched to achieve its maximum hardness and toughness. The high carbon and chromium content of D2 allow it to maintain its hardness even when cooled slowly, making it suitable for air-quenching. Vacuum-quenching further improves the mechanical properties of D2 by reducing residual stress and preventing warping.
O1 vs D2 Tool Steel – 3. Properties
The compositional and heat treatment differences between O1 and D2 tool steel result in distinct material properties. O1 steel has high hardness and wear resistance, making it suitable for cutting tools and punches that require resistance to abrasive wear. It also has good edge retention and can be sharpened to a fine point. However, O1’s toughness is lower compared to D2, making it less suitable for impact-loaded applications.
D2 steel, on the other hand, offers a combination of high hardness, wear resistance, and toughness. Its high carbon and chromium content give it excellent resistance to heat and corrosion, making it suitable for high-temperature applications and environments with corrosive elements. D2’s toughness allows it to withstand impact loads better than O1, making it ideal for punches, dies, and cutting tools that experience both wear and impact.
O1 vs D2 Tool Steel – 4. Applications
The choice between O1 and D2 tool steel depends on the specific requirements of the application. O1’s high hardness and wear resistance make it well-suited for applications that involve severe abrasive wear, such as cutting tools for non-ferrous metals, woodworking tools, and punches for light to medium-duty applications. It is also commonly used in knives and other cutting implements that require a sharp, long-lasting edge.
D2 steel, with its combination of hardness, wear resistance, and toughness, is ideal for applications that demand both durability and impact resistance. It is widely used in punches and dies for stamping and forming operations, cutting tools for tough materials like stainless steel, and wear parts in high-pressure and high-temperature environments. D2 is also a popular choice for knives and other cutting tools that require durability and resistance to corrosion.
O1 vs D2 Tool Steel – 5. Cost
Cost can also be a factor when considering O1 vs D2 tool steel. Generally speaking, D2 steel tends to be more expensive than O1 due to its higher alloy content and more complex heat treatment process. The added properties of D2, such as its superior toughness and resistance to heat and corrosion, often justify the higher cost in demanding applications. However, for applications where wear resistance is the primary concern and impact loads are minimal, O1 may offer a more cost-effective solution.
Conclusion
In summary, O1 and D2 tool steel differ significantly in composition, heat treatment, properties, and applications. O1 steel, with its high hardness and wear resistance, is well-suited for applications that involve severe abrasive wear, while D2 steel offers a combination of hardness, wear resistance, and toughness that is ideal for impact-loaded and high-temperature applications.
Thank you for reading our article and we hope it can help you to have a better understanding of the differences between O1 vs D2 tool steel. If you are looking for O1 & D2 tool steel suppliers online now, please don’t hesitate to contact Huaxia Steel.
As a leading supplier of tool steel products from Shanghai, China, Huaxia Steel provides customers with high-quality tool steel, carbon steel, alloy steel, carbon steel tubes, and carbon steel pipes at a very competitive price.