Tool steel, as a crucial type of metallic material, plays a pivotal role in industrial production due to its exceptional hardness and wear resistance. However, the rapid cutting wear of tool steel often impacts its service life during usage. Consequently, optimizing and enhancing the cutting performance of tool steel is imperative. In this article, we will take a closer look at the optimization of cutting performance of tool steel.
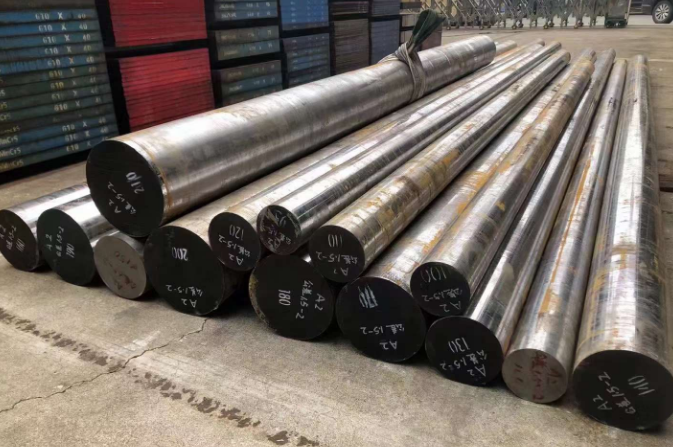
Optimization of Cutting Performance of Tool Steel:
Firstly, selecting high-quality raw materials is fundamental to improving the cutting performance of tool steel. Since tool steel primarily comprises iron, cobalt, nickel, steel, and other materials, employing superior processing materials during tool steel manufacturing can reduce impurity content, thereby enhancing its hardness and cutting performance, ultimately extending its service life.
Secondly, optimizing the chemical composition is crucial. The chemical composition of tool steel significantly affects its cutting performance. For instance, adding vanadium, titanium, and other alloy elements to tool steel can refine its microstructure, mitigating fractures or damages during cutting, thereby improving its cutting performance. Furthermore, optimizing the chemical composition also enhances the welding properties and heat treatment stability, ultimately enhancing work efficiency and product quality.
Thirdly, surface treatment is a vital method for improving the cutting performance of tool steel. Surface treatment techniques can modify the material’s chemical properties and characteristics, such as cutting performance, wear resistance, toughness, and fatigue resistance. Common surface treatment methods include chromium plating, electroless plating, polishing, sandblasting, among others. For example, chromium plating on the surface of tool steel can increase its hardness and wear resistance, thereby enhancing its cutting efficiency and service life.
Additionally, heat treatment is essential. Advanced heat treatment techniques can refine the grain size and microstructure of tool steel, thereby enhancing its strength and cutting performance. Common methods include quenching, carburizing, etc. For instance, carburizing involves heating and holding tool steel in a carburizing medium to allow carbon atoms to penetrate its surface. This process not only increases the carbon content on the steel’s surface but also modifies its microstructure and properties, ultimately enhancing its cutting performance.
Conclusion
In conclusion, tool steel, with its unique properties and diverse applications, holds a significant position in modern industries. To improve production efficiency and reduce costs, optimizing the cutting performance of tool steel can be achieved through selecting high-quality raw materials, optimizing chemical composition, implementing surface treatment, and utilizing heat treatment. In practical applications, selecting the most suitable optimization method should be based on specific cutting scenarios and operational requirements.
Why Choose Tool Steel?
Thank you for reading our article and we hope it can help you to have a better understanding of the optimization of cutting performance of tool steel. If you are looking for suppliers and manufacturers of tool steel, we would advise you to visit Huaxia Steel.
As a leading supplier of carbon steel from Shanghai China, Huaxia Steel offers customers high-quality carbon steel, tool steel, and alloy steel at very competitive prices.